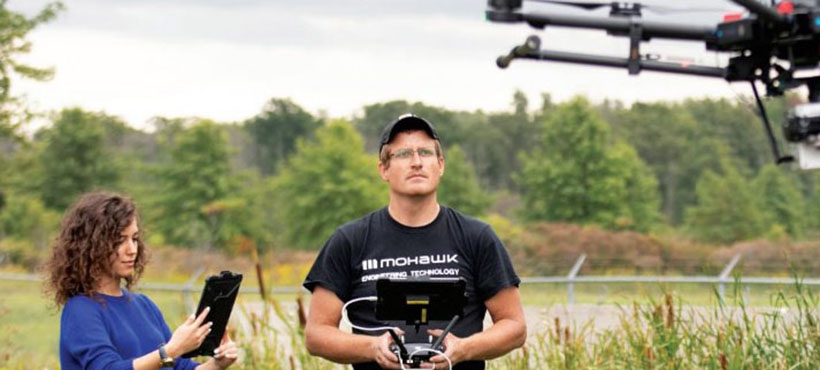
ArcelorMittal employs approximately 168,000 employees in 60 countries. Flagship locations like ArcelorMittal Dofasco play a vital role in inventing smarter steels for a better world. Each year, they ship 4.5 million net tons of high-quality flat carbon steel. And they partner with the top automotive, energy, packaging and construction brands to develop lighter, stronger and more sustainable products – from cans to cars.
Funder: ArcelorMittal Dofasco
Research Area: Unmanned & Remote Sensing
Research Team: Richard Borger, Matthew Shelley, James Kretz
Future Ready Challenge
Industrial manufacturing facilities require that equipment and infrastructure be regularly maintained, and the newest technologies adopted. This type of work traditionally requires an engineering team to visit the site, take measurements, and complete regular inspections of the existing infrastructure.
However, site visits are often time-consuming to organize, as the engineering team must coordinate with contractors and on-site workers, and the visits frequently require personnel to enter difficult to access areas in addition to requiring equipment shutdown.
R & D Collaboration
To reduce the hazards and technical challenges necessitated by engineering site visits, ArcelorMittal Dofasco reached out to the Unmanned and Remote Sensing Innovation Centre (URSIC) at Mohawk College to explore if remote sensing technology could be used to create a LiDAR-point cloud map of the facilities. Having access to highly accurate mapping of its facility allows the ArcelorMittal Dofasco engineering teams to potentially reduce the need for site visits.
Innovative Results
The URSIC team worked on-site at ArcelorMittal Dofasco in Hamilton, Ontario to conduct the scans needed to create a proof-of-concept map of the facilities. First the URSIC team utilized a Matterport Leica BLK360 and Leica P20 scanner to create a colorized point cloud of the Tin Mill at Dofasco, including the outfeed roller stands. This location was an ideal first location to capture as it was low in environmental dust and contaminants that could reduce the efficacy of the equipment. After achieving excellent results for all LiDAR scans in the Tin Mill, the URSIC team and AMD staff chose to tackle a more challenging area.
The URSIC team next attempted to complete a LiDAR scan using the same equipment in Blast Furnace 4. In this area, the equipment would be challenged to scan a dark area with significant dust. The team was unsure if the equipment would perform properly in this environment, or if the dust would reduce the accuracy of the scanning equipment.
After an initial test in Blast Furnace 4 yielded outstanding results, the team moved on to successfully scanning additional levels of the area from the stock house up to the highest level of the furnace that could be accessed without requiring specialized PPE.
Once the data was collected, the URSIC team registered the scans into an accurate, colorized point cloud which could be uploaded to a server and distributed by ArcelorMittal Dofasco as needed for future projects within these areas. By completing this proof-of-concept project for the ArcelorMittal Dofasco team, the applied research project has showed how this technology can reduce the need for site visits by ArcelorMittal Dofasco engineering teams, creating potential savings in project planning costs.
“The Unmanned and Remote Sensing Innovation Centre at Mohawk College provided valuable expertise in a wide range of LiDAR scanning tools and was able to produce extremely accurate digital maps of our facilities,” Darren Martin, Discipline Engineer Manager, ArcelorMittal Dofasco. “We have been very impressed with the results.”
Read more here about Mohawk College working with ArcelorMittal Dofasco in 2019 on 3D modelling (see page 6).