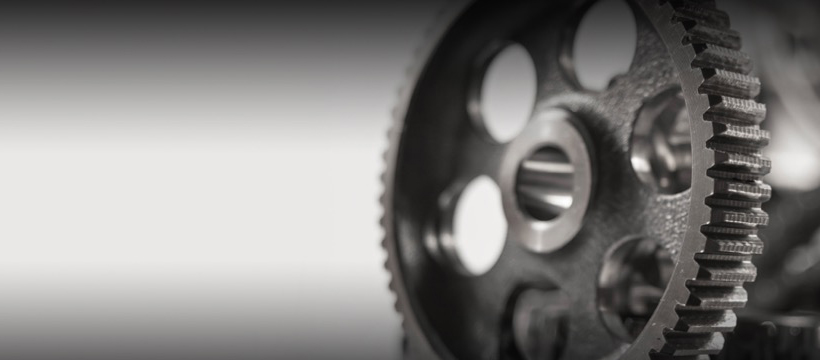
The Grandfield Research Group at Hamilton’s McMaster University focuses on the development and multi-length scale characterization of biomaterials for bone interfacing applications in orthopedics and dentistry. The Grandfield Research Group asked the Additive Manufacturing Innovation Centre to collaborate with them to evaluate the suitability of Ti-553, a titanium alloy, for use in 3D printed implants.
Future Ready Challenge
Additive manufacturing has allowed the medical industry to rethink how it approaches the manufacturing of medical implants. With its ability to allow for the detailed customization of implants, often at a faster speed of production, additive manufacturing is considered to be a game-changer. However, the use of additive manufacturing in healthcare is still in its early stages; Health Canada only released their 3D printed medical device guide in November 2018. Scholarly research in the field is crucial to the development of guidelines and best practices for clinical usage.
R & D Collaboration
The Grandfield Research Group at Hamilton’s McMaster University focuses on the development and multi-length scale characterization of biomaterials for bone interfacing applications in orthopedics and dentistry. Under the leadership of Dr. Kathryn Grandfield, the research team is pioneering the investigation of bone-implant interfaces in order to improve implant success and to improve understanding of healthy and pathological bone.
Most 3D printed implants are manufactured using the Ti64 titanium alloy powder. The Grandfield Research Group asked the Additive Manufacturing Innovation Centre (AMIC) to collaborate with them to evaluate the suitability of Ti-553, a titanium alloy, for use in 3D printed implants. The research team at AMIC frequently collaborates with university researchers who require applied expertise in materials development for metal additive manufacturing.
Innovative Results
The McMaster University research team wanted to understand if the topography (or surface features) of Ti-553 could improve the osseointegration (the process of creating bone ingrowth) of implants. Because Ti-553 is not a commercially available material for Direct Metal Laser Sintering (DMLS), they partnered with Mohawk College to produce the metal samples needed for the research study. Mohawk validated the additive manufacturing process parameters needed to produce components from this novel material and manufactured geometrically simple samples for the study using an EOS metal 3D printer.
"Working with AMIC has been instrumental in bringing our innovations to life," says Dr. Grandfield. "We used their facility to produce 3D-printed biomaterials for research and industrial collaborations, not only quickly, but with the added value of their expertise in additive manufacturing."
Mohawk was able to provide the Grandfield Research Group with specialized expertise to accelerate and support their important medical research. Additionally, this research represents the first time that Ti-553 has been evaluated for use as a metal medical implant. The research from confirms that new combinations of materials and manufacturing techniques can improve the chance of osseointegration. The research findings, authored by Chiara Micheletti, Bryan E. J. Lee, Joseph Deering, Dakota M. Binkley, Simon Coulson, Asad Hussanain, Hatem Zurob and Kathryn Grandfield, were published in Nanotechnology Volume 31, Number 23 and are available for download.