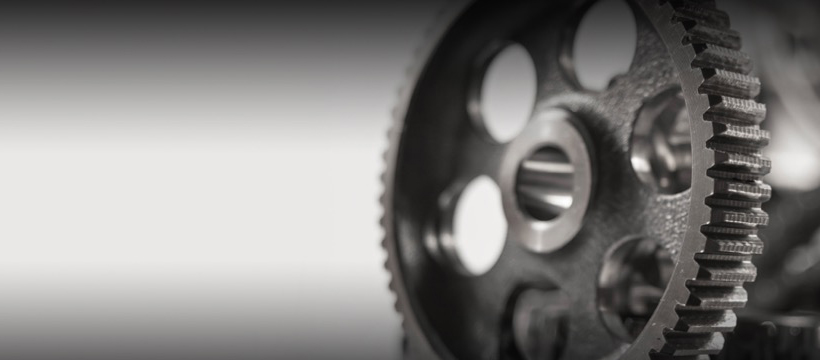
Merq Automation, based in Stoney Creek, is a laboratory solutions and automation company. Merq asked the Additive Manufacturing Innovation Centre to partner with them in the design and development of an ergonomic syringe dispenser.
Funder: FedDev Ontario (SONAMI)
Research Area: AMIC
Research Team: Jeffrey McIsaac, Alex Cook, Grant Wingfield, Sierra Robinson
Future Ready Challenge
In food, chemical and environmental labs, a syringe is a crucial tool for dispensing and transferring liquids. But it is also a tool that must be used with precision and care, especially when working with liquids that are high in particulate matter. The process of using a syringe can be physically difficult for lab technicians who must repeat the process over and over again; the dispensing or transferring of liquids can take a long time to complete while the repetition of the process increases the possibility of inaccurate measurements due to human error and increases the risk of health and safety concerns due to repetitive strain injuries.
R & D Collaboration
Merq Automation, based in Stoney Creek, is a laboratory solutions and automation company. The company provides equipment, design and automation support to food, environmental and chemistry labs across Canada. Committed to innovation in its field, the company realized that there was an opportunity to develop a new product that would help lab technicians improve their accuracy when working with small quantities of liquids. Merq Automation asked the Additive Manufacturing Innovation Centre (AMIC) to partner with them in the design and development of an ergonomic syringe dispenser.
Innovative Results
The AMIC research team designed and built multiple iterations of the syringe dispenser, testing the product at each stage for ease of use, safety and functionality. By using a combination of Fused Deposition Modeling (FDM) and Selective Laser Sintering (SLS), the team were able to produce the plastic prototypes quickly while also minimizing plastic waste. Functional considerations of the product design included finding quality internal components that fit inside the pneumatic system, achieving the right tolerances necessary for the moving components and designing the quick release system that connects the syringe to the pneumatic system. The research team also designed the product to include raised caution lines and built-in instructions (such as an arrow with the word ‘release’) to support user safety and the correct usage of the product. In addition to the product design and development, the AMIC team also provided recommendations for production considerations such as material costs and printing time.
As a result of the collaboration between Mohawk and Merq, the company's clients can now purchase a product that will decrease health and safety risks due to repetitive strain and improve productivity by reducing the time technicians spend dispensing and transferring samples. They also gained a new employee: Merq hired one of the student researchers that worked on the research project. The Ergonomic Syringe Dispenser is now available for sale to labs across the country.